Propellers of high quality and good balance has not been easy to find for drones in the Crazyflie size. Not that long ago HQ-prop released a propeller, 51MMX2GR-1MM-PC, with 51mm in diameter (2 inch) that could work well for the Crazyflie 2.1. HQ-prop is famous for making good propellers for FPV-drones and them releasing a 51mm propeller was quite exciting as this could be used on the Crazyflie. After getting some samples we tested them with a couple of different 7x20mm coreless bushed motors with different rpm/v (KV) values until we found a good match, a 13400 KV motor. With this motor the maximum thrust of a Crazyflie using a new charged battery reaches ~80 grams. This is ~40% more thrust then the stock Crazyflie 2.1 with a 60 grams of total maximum thrust. It does come at an expense of efficiency though and the hover time is reduced from ~7:00 to ~6:00 minutes.
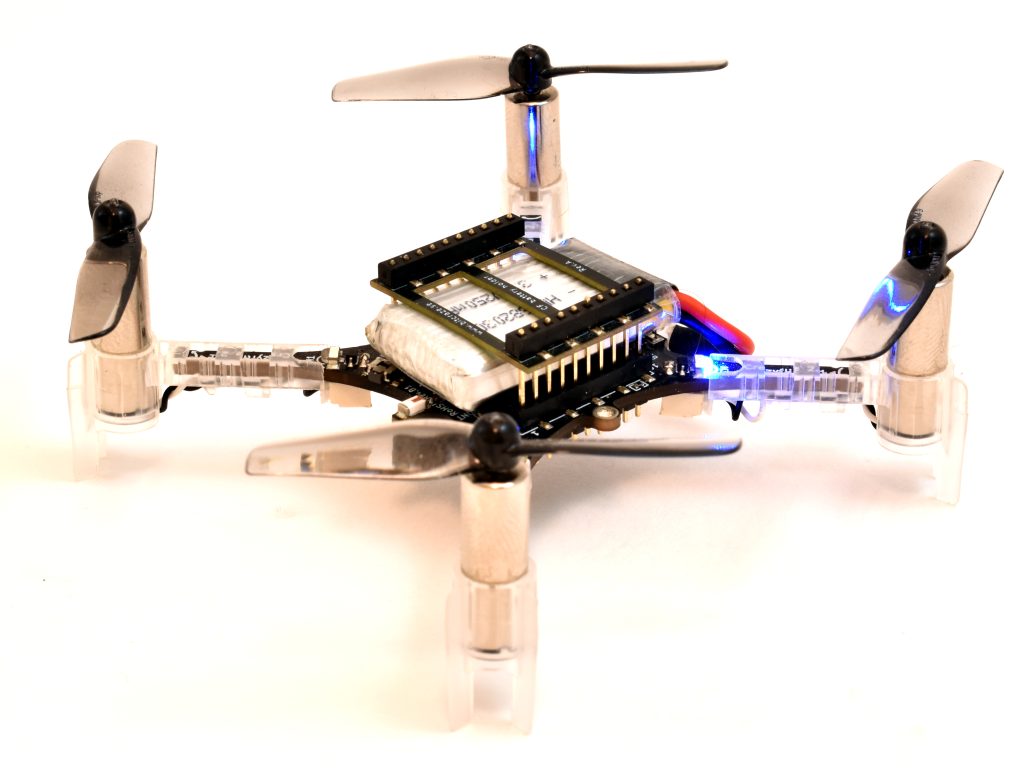
Using the thrust stand we wrote about and built earlier we can get an estimated value of the efficiency which is interesting in many aspects.
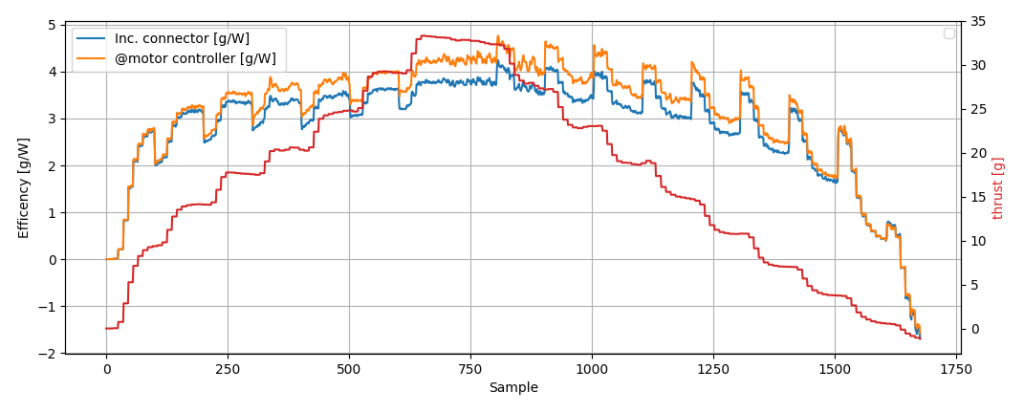
Instead of ramping up/down the PWM in very small steps as was done in the thrust stand post, the same test has been changed to do it in larger steps to make it easier to separate the changed efficiency effect when doing acceleration/deceleration. Another thing to note is that in this test the PWM was only ramped up to 50% as the RPM measurement sensor had trouble tracking the transparent-grey propeller at higher speeds. There are two lines graphing the efficiency where the blue line is the one including the losses in the connector which should be closest to the real overall efficiency. Following the blue line we can see that at ~33 grams of thrust we get ~3.8 g/W. Very similar to the stock Crazyflie 2.1 setup with 45mm propeller and 7×16 mm motor.
So if you are in a need for some more thrust because you are using many decks, or maybe just because you want more agility, be sure to watch out for the thrust upgrade kit that will be released during the fall!
IROS
The two coming weeks are going to be a little special for us: as written before, we’re going to Japan ! Kimberly is already there for ROSCon, but we will have a booth at IROS. If you’re there, don’t forget our tech meetup on Monday 24th of October at 16.00 at our booth 59.
The whole company is going there, so there may be some delays in handling emails and shipping from the end of this week.